Large global manufacturers were among the earliest adopters of digital document management solutions. Today, companies of every size are facing strong competitive pressure, supply chain woes and a rapidly changing regulatory landscape. Manufacturers need to be innovative to get their products to market faster, compete in global markets and become low-cost producers while delivering superior quality and customer service.
By its very nature, manufacturing is document-intensive. It often requires that documentation follow a product through the complete product lifecycle. Then, it must be stored securely and available for quick access for customer service, audits and other purposes. Without digitization, employees waste time capturing, storing, and routing documents to others using slow manual processes. There’s also a lack of insight into potential bottlenecks and opportunities for process improvement.
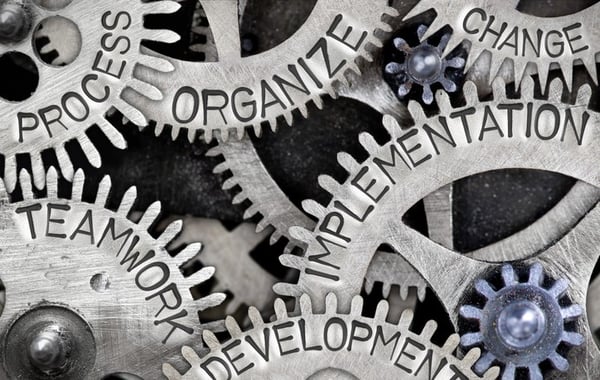
It’s a tall order, and that’s where cloud-based document management comes in. It enables small and mid-sized manufacturers to access technology resources that were once only available to their larger counterparts — and still stay within their budgets. With DocuWare Cloud, all documents pertaining to a production, logistics or accounting process are digitized and stored in a central archive. Whether working with design drawings, material orders, production documents, sales orders or invoices, employees can access all documents 24/7 in the office or at home. Instant access enables your company to reduce risk, expedite production and contain costs.
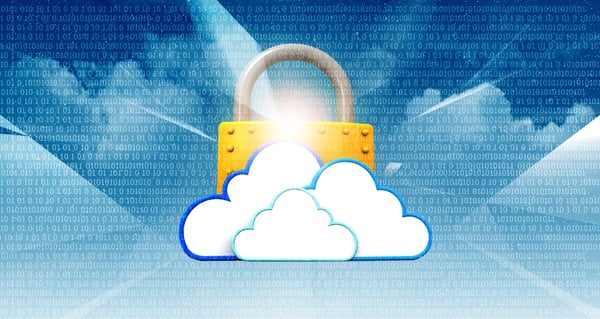
DocuWare Cloud can also handle every facet of information security. Your company can restrict unauthorized viewing of confidential documents and develop guidelines to protect proprietary information as well as ensure customer data security. You’ll also be able to prove compliance with Environmental Protection Agency (EPA), and Occupational Safety and Health Administration (OSHA) regulatory requirements and counter cyberthreats with state-of-the-art encryption of data, documents and online communication.
Filling open positions is another high-priority issue facing manufacturers. In their 2022 Manufacturing Industry Outlook, Deloitte notes that record numbers of unfilled jobs are likely to limit higher productivity and growth in 2022. And last year they estimated a shortfall of 2.1 million skilled jobs by 2030. Document management’s automated workflow reduces time spent on manual tasks and improves collaboration to help you make the most out of your workforce’s skills, even if the number of employees is smaller than you would like due to the tight labor market.
Check out these manufacturing success stories
The manufacturing sector spans many types of companies from metal fabrication and machine parts to biotechnology and pharmaceuticals. What do they have in common? And how does DocuWare help its manufacturing customers to work smarter? Here are a few cases in point.
Audit proofing a manufacturer in a highly regulated industry
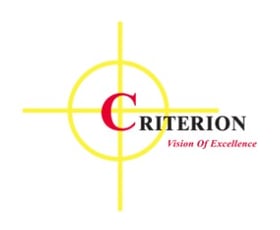
DocuWare was implemented to digitize thousands of existing and new documents, which are now available at the click of a mouse – saving employees from tedious searches and reducing stress when compiling documents during audits. Prior to DocuWare use, audit preparations took several hours, but now the documents can be found easily by inputting job numbers and retrieving the records. Having the information available instantly also greatly reduced employees’ stress levels during audit preparation time. Ultimately, all of this time saved led to increased productivity.
The company uses DocuWare for a variety of needs, including retaining documents for the FDA, their quality management system, preventative maintenance on machines and equipment, storing employee and client records and for external documents used by the quality department for their customers. The company also installed DocuWare stations on its shop and office floors so that employees could be trained to retrieve records electronically rather than printing them out. According to the company’s internal records, using DocuWare helped save 41 trees just this year and several hundred dollars in paper costs.
Avoiding the hazards of paper-based invoice processing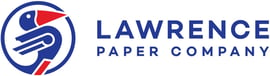
Lawrence Paper Company produces boxes and packaging materials. In 2021, it made enough corrugated sheets to circumnavigate the globe. Digitizing documents and eliminating paper pushing between departments brought immediate benefits to the accounting department.
For example, prior to DocuWare, a purchase order created a paper trail that was often hard to follow. It would circulate between seven employees and then was stored in a file cabinet where it could be lost or misfiled. DocuWare was integrated with the company’s ERP system and streamlined this task and other accounting processes. As a result, they went from processing 15 invoices a day to processing 100 of them.
Employees particularly enjoy working with DocuWare Intelligent Indexing which allows them to automatically index and file documents from the company’s internal reporting software. To celebrate their paperless status, employees held a big shredding party. Then they were able to get rid of file cabinets and free up office space.
Integration between DocuWare and an ERP system supports quality control
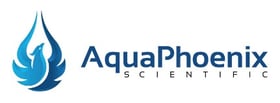
Today, when an order is received online or via phone, it is entered into AquaPhoenix’s ERP system and a sales order number is generated. Using Intelligent Indexing, the information from the sales order automatically populates the index fields in DocuWare, eliminating double entry. This sales order is then used to route the order through the test kit assembly process.
The manufacturing department follows a similar process when tracking the production of chemicals or reagents. They maintain a strict quality control process documented by a work order, which is created in their ERP system and then used to record production times, quality checks, and batch and lot numbers. At the end of the process, the completed work order is scanned into DocuWare where it is automatically indexed and stored and becomes part of the company’s quality control documentation.
Secure recordkeeping helps get compliance under control
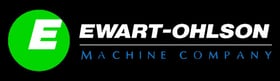
Before DocuWare, all records and paper documents had to be sorted manually and filed in a physical location. When staff in Quality Control or any other department needed to reference the documents or respond to customer requests, the search was frustrating and time-consuming.
Since digitization, file retrieval, which used to take upwards of 30 minutes per search, can be done in under a minute. Securely storing and retrieving files electronically has increased the speed of business processes companywide. Ewart-Ohlson is a small business with a staff of twenty, so it’s particularly important that they can channel more resources toward increasing production efficiency, quality control, customer service and other activities that affect the bottom line.
Why does choosing DocuWare makes sense?
DocuWare customers securely archive documents and retrieve them instantly, but that’s just the beginning. They achieve additional ROI when they build workflows around manufacturing processes that reduce rework, speed up accounts payable and receivable and gain insight into potential bottlenecks. Controlled access, task lists and email notifications enable your staff to handle daily responsibilities more efficiently and decision makers to approve, reject or request more information along checkpoints in all your processes.
Since DocuWare Cloud is sold by subscription, you can start small and expand your document management solution as your business grows. By implementing DocuWare Cloud, your company will be able to adapt to changing circumstances and safeguard future profitability. Want to learn more? Request your free demo.
Editor’s note: This post has been updated for accuracy and new content has been added.